「見える化」って気持ち悪い!?可視化とは違うの?見える化を徹底解説!!
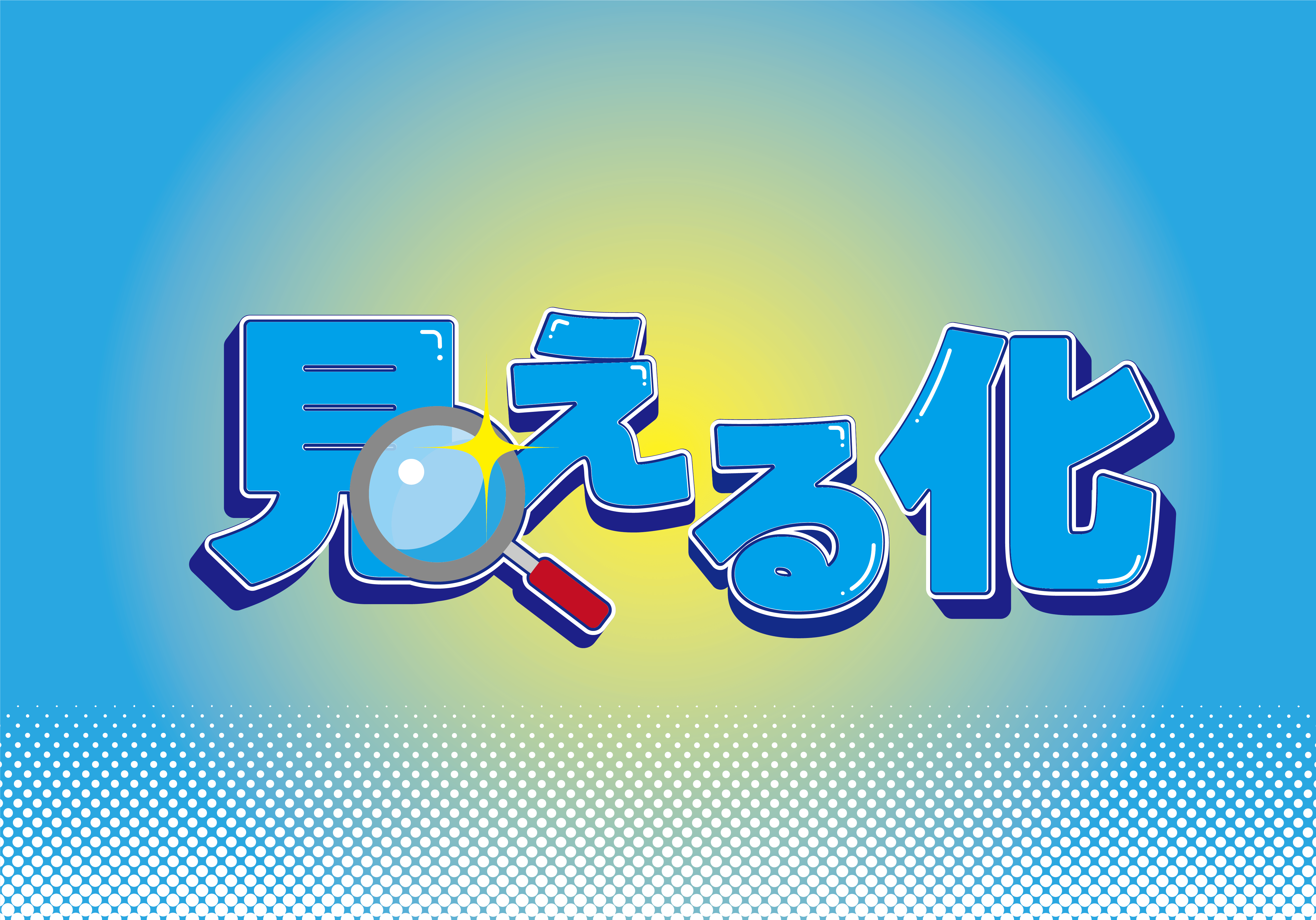
「見える化」という言葉を、よく耳にします。グラフや図にして、他の人にもわかりやすいようにしました。しかし、業務は何も変わりません。実はその「見える化」、まちがっていたのです。
今回は、みんな間違えて使っている「見える化」について、説明いたします。
目次
「見える化」って気持ち悪い?
「見える化」という言葉に、違和感を覚える人もそう少なくないのではないでしょうか。
見える化は、「見える」という自動詞と、「○○化」という接続語から成る言葉です。そもそも「○○化」は漢語の名詞に使われる接続語で「映画化」「高齢化」のように使われます。本来名詞の入るところに自動詞が入っているのが違和感の原因なのではないでしょうか。
しかし「見える化」自体が名詞になっているため、業務改善方法として定着させるためにわざと印象に残りやすい言葉にしているのかもしれません。
また見える化はしばしば「可視化」と同じ意味の言葉として使われます。しかし、「可視化」と「見える化」は違う言葉なのです。
「見える化」を理解することで、気持ちよく「見える化」という言葉を使えるかもしてません。
見える化とは
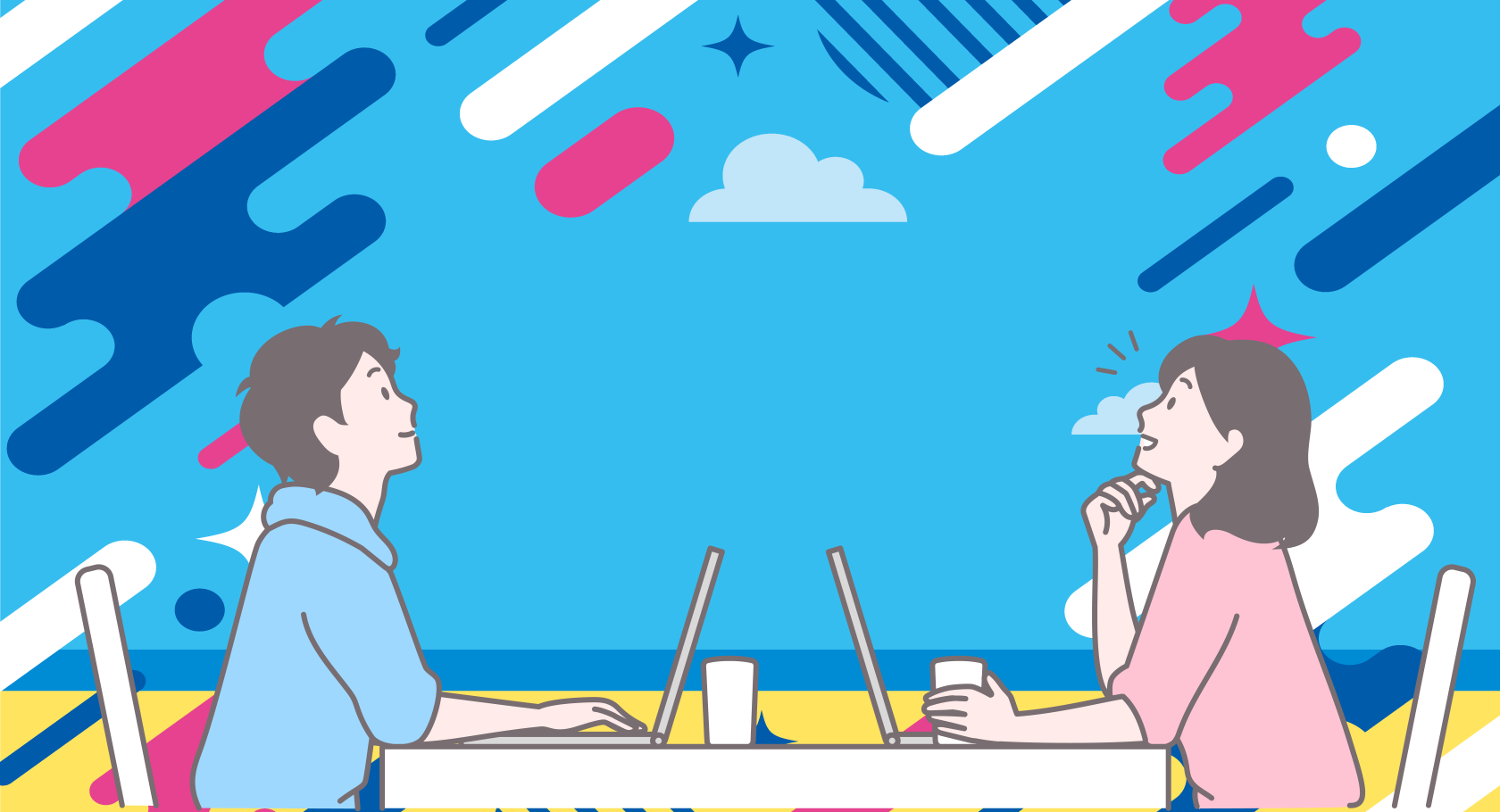
見える化とは、目には見えないものを目に見えるようにすることを言います。
「見える化」という言葉は、1988年にトヨタ自動車株式会社所属の、岡本渉氏が発行した論文「生産保全活動の実態の見える化」にて初めて登場しました。
トヨタ方式の見える化
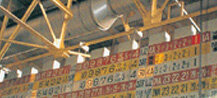
トヨタの見える化で一番代表的なものが「あんどん」です。
トヨタ生産工場では、「目で見る管理」が重視されており、その方法として設備の稼働状況や作業指示が一目でわかる「あんどん」と呼ばれるランプを採用しています。
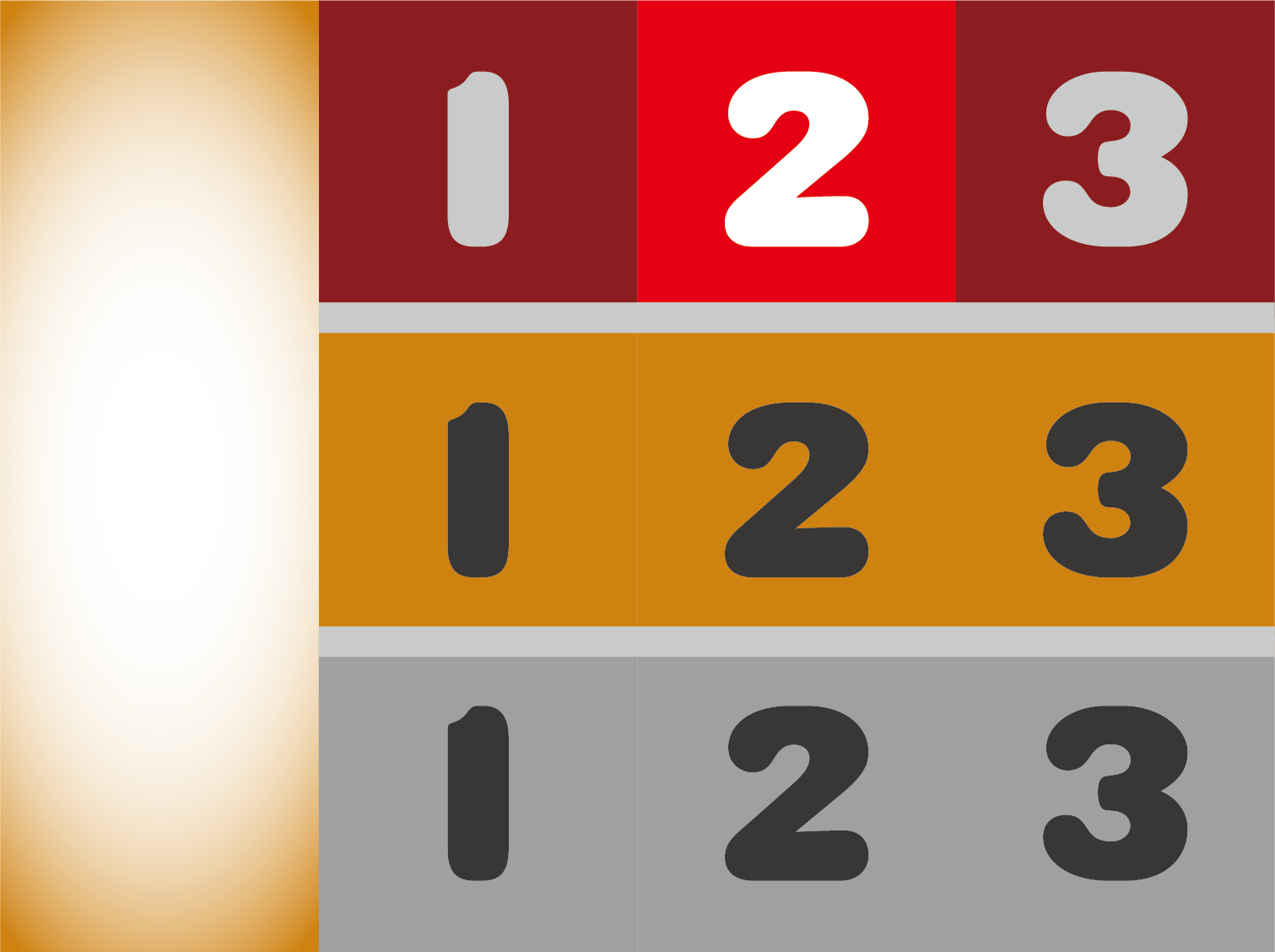
たとえば工場の製造ラインにて、故障などにより機械が停止した場合、自動で「赤」のランプが点灯します。担当者はあんどんの赤ランプを見て、機械の点検を行います。異常での停止の場合は調整・点検を行い、管理者は原因について徹底的に調査し異常の再発防止を行います。
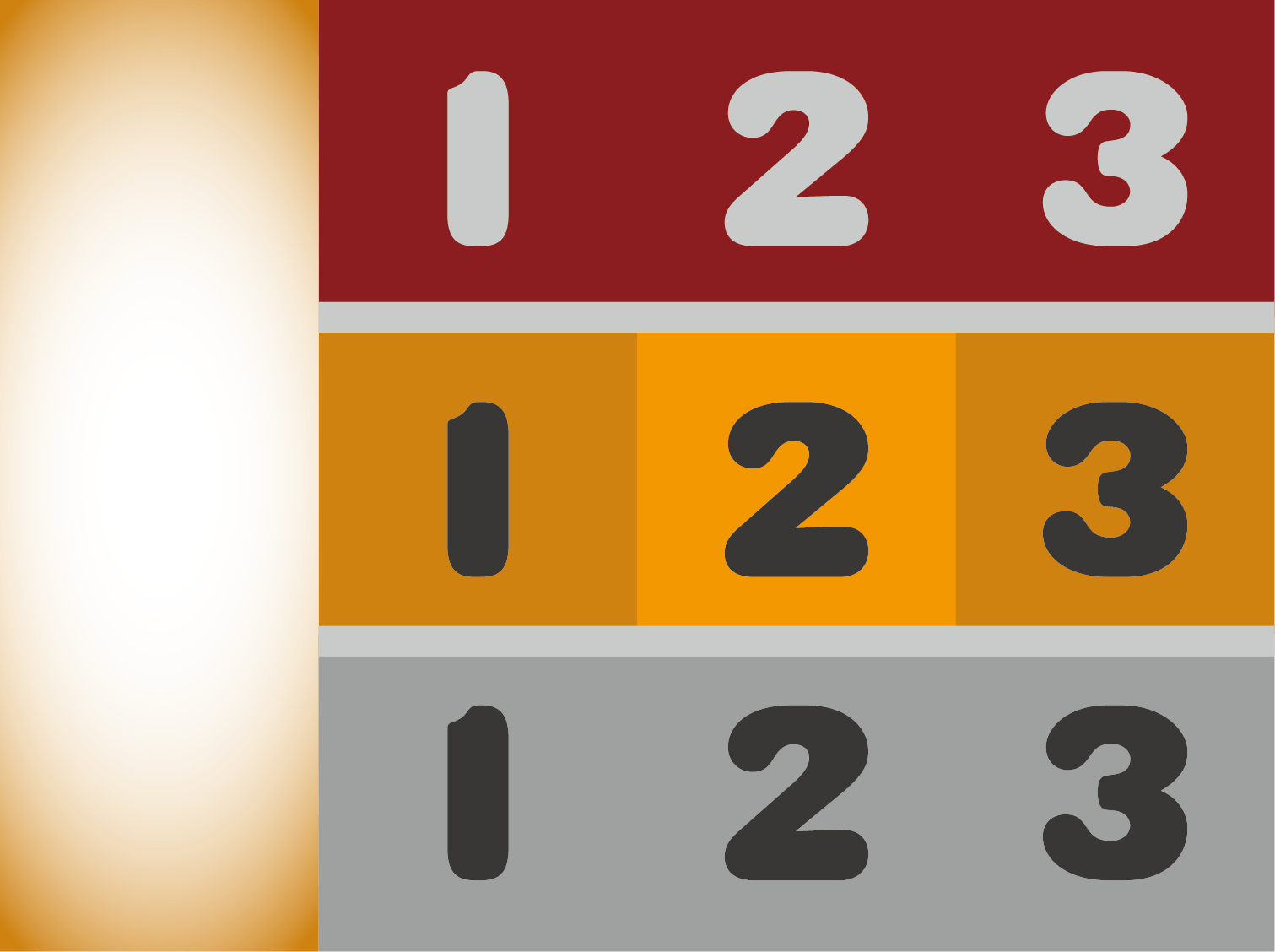
工具・刃物の交換や品質確認の時点で、自動的に「黄」が点灯して機械が停止します。担当者は機械の指示に従い、あらかじめ準備されている新しい工具・刃物との交換や品質確認を行い、作業終了後に機械を再起動します。
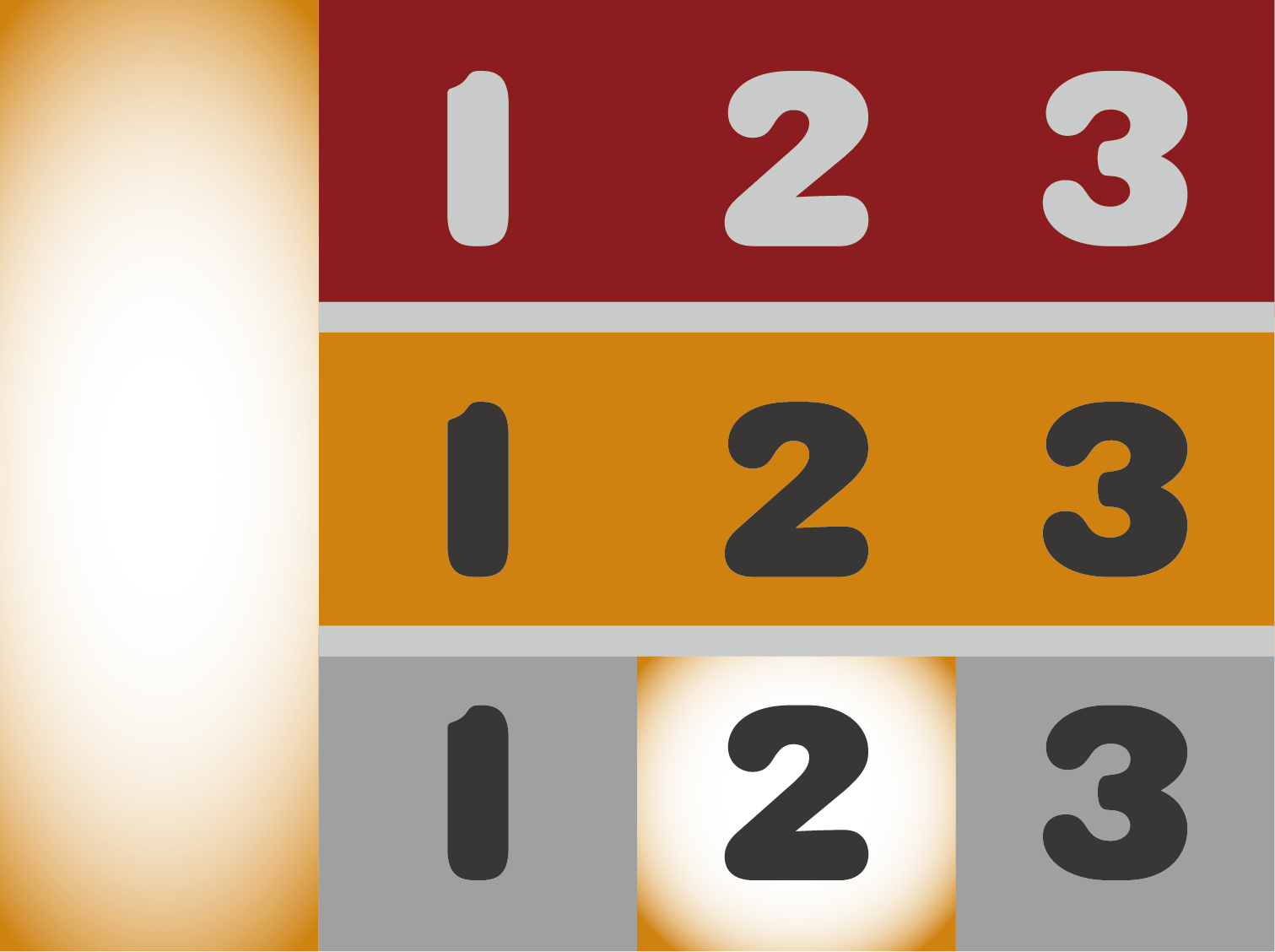
また工具交換や品質確認の際に担当者が機械を操作すると、あんどんの「白」が点灯します。その点灯によりその機械で作業を行っていることを関係者に通知します。
「見える化」と「可視化」
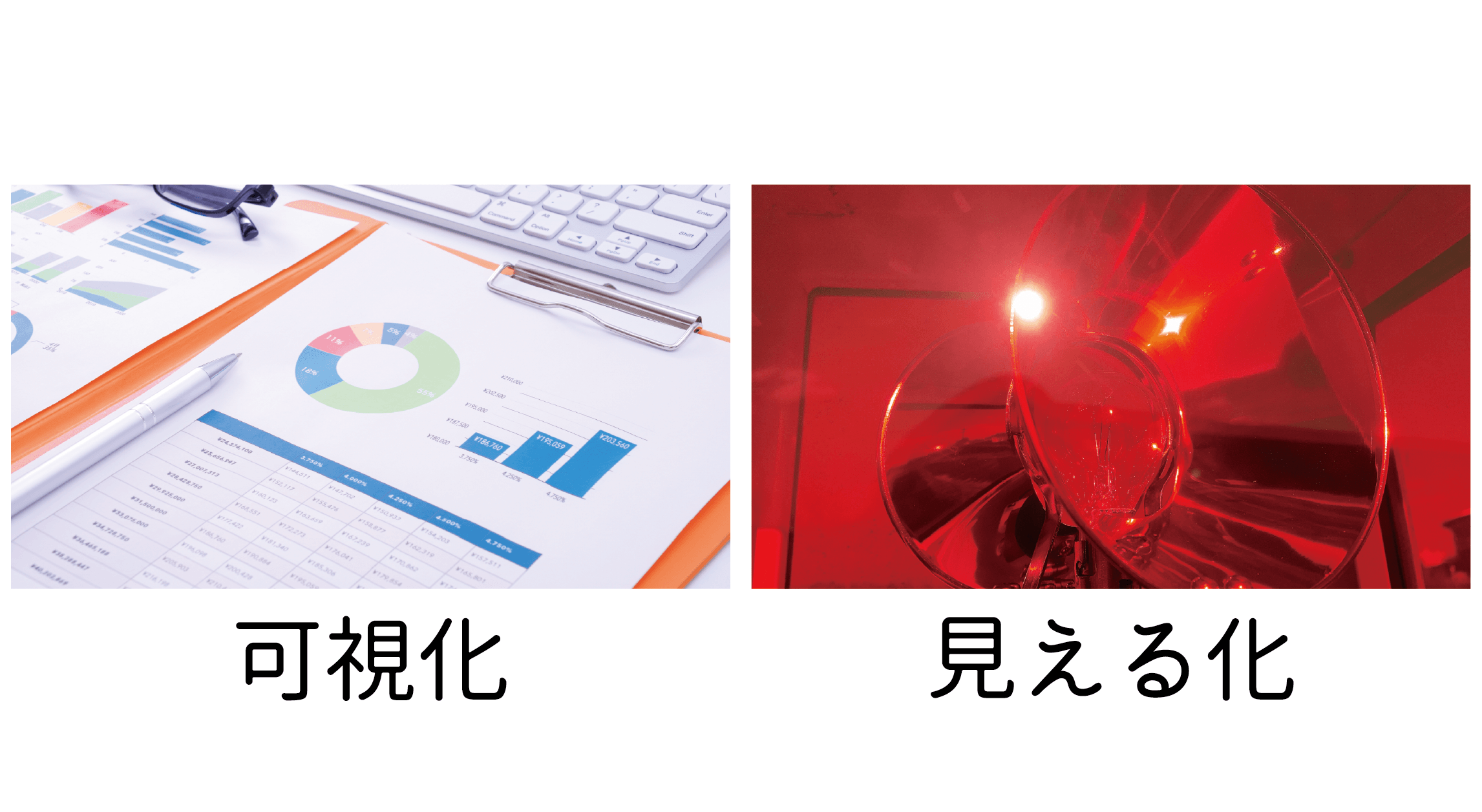
可視化のゴールは「目に見える形にすること」です。しかし、見える化のゴールは「問題点の判断基準が共有されており、問題・課題の改善が繰り返し行われる状態」なのです。
例えば、コンビニの場合商品の在庫数がわかるように管理表を作りました。これが可視化です。
補充する際に「補充した数と在庫数を管理表に記入し、在庫数が100個を切ったら発注を行う」ようにルールを作りました。これが見える化なのです。
このように可視化では見やすくはなりましたが見落としが起こってしまいます。見える化のように必ず見て発注まで行うルールを作れば見落としは起こりません。
見える化のメリット・デメリット
メリット
メリットは「問題点の判断基準が共有されていること」ではないでしょうか。
異常が起こる場合に多いのは独自の判断基準による見落としです。
「まだ大丈夫だろう」「どうにか動いているから問題ないだろう」のような判断をしていると大きな事故につながってしまいます。その判断基準が共有されており全員が状況を把握できる状態であれば、業務をより効率的に行うことができます。
デメリット
大きなデメリットは「作業量が増える」ことです。
先程のコンビニでの例では、ルールにより「管理表に補充した数を書き込む」手間が増えています。
また作業が増えるのはその作業を行う人だけで、組織の上層部は特に作業の負担はありません。そういった不満の種が増えてしまうのも見える化の難しい点なのではないでしょうか。
見える化できるモノ・コト
異常の見える化
トヨタの例がこちらにあたります。
見える化することで、異常が起こる回数を減らす、もしくは無くすことができます。また異常を無くすためのより良い手順・やり方が全員の共通認識となるため、より効率よく業務を行うことができます。
ノウハウの見える化
職場に「仕事が早く終わるがミスが多い人」と「仕事は遅いが質のいい人」がいた場合、二人のいいとこ取りをすればよいでしょう。その「いいところ」が「ノウハウ」になります。「仕事が早く終わる方法」と「ミスをしない方法」を二人は持っているはずです。その「ノウハウ」を共有するためには「見える化」が重要です。
業務の見える化
今一番近くの席に座っている人がどんな業務をしているかわかりますか?
どれくらいの仕事を請け負っているかわかりますか?
これらがわからないと、無理な作業量を任されている社員や業務の無駄が出てしまいます。
これを放置すれば、効率の低下や最悪の場合過労死などの原因になってしまいます。
組織の見える化
組織とは「目標を達成するために集まった集団」のことを指します。しかし目標が明確に共有されていないと、個々がバラバラで連携のできない集団になってしまいます。組織は同じ目標に向かって個々の力を合わせるからこそ組織の力となります。
組織の目標を見える化すれば、組織としての本来の力を発揮することで、あらたな価値・利益を生むことができるのではないでしょうか。
見える化を行うためには…
デメリットでも上げた通り、見える化を行うと「作業量が増えてしまう」のが大きな問題になってしまいます。
それを解決するのがIT技術です。
IT技術を活用すれば、作業量を減らす・または作業自体を無くすことができます。
例えばセンサーなどを用いれば、個数の自動カウント、また個数の表示を行うことができます。
これで従業員が、個数を数える手間を減らすことができました。
また見える化のために、「つねに見える状態」にすることが重要です。従業員が意図的に見に行かなければいけない状況では、見える化とは言えません。
センサーで読み取った異常値を、デジタルサイネージやパトランプで通知することで、誰でも目に入る状態になり、見える化の第一歩になります。
見える化を推進する場合は同時にITツール・IT設備も同時に検討しましょう。
まとめ
今回は実は難しい「見える化」について解説しました。
見える化はトヨタから生まれた言葉で、「問題点の判断基準が共有されており、問題・課題の改善が繰り返し行われる状態」を言います。良いことも悪いことも全員に共有されるため、良いことは真似して、悪いことは改善を行うことができます。
皆様も自身の業務を見直して少しずつ見える化を行ってはいかがでしょうか。
ご質問・ご相談に関しては
こちらからお問い合わせください。