ファクトリーNYC 株式会社ナカヨ 前橋工場見学に行ってきた
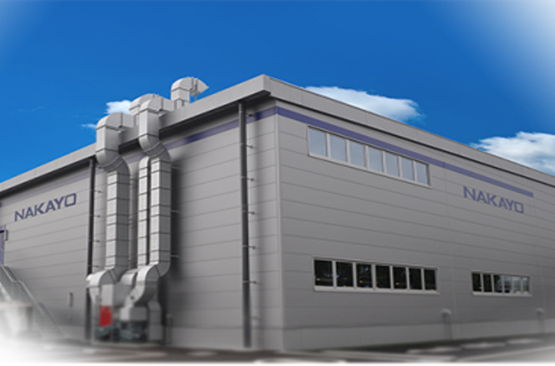
通信機器総合メーカーとして、創業78年の株式会社ナカヨ 前橋工場を見学してきました。
時代の変化、ニーズに対応したモノづくりとして、通信機器からIoT・生産受託等、様々な製品を製造しています。
今回、株式会社ナカヨが製品化した、自社工場でも活躍しているファクトリーNYCを紹介したいと思います。
目次
設備維持の課題
工場内には、様々な設備機器が稼働していました。全自動成型機、半田DIP槽、ターレットパンチプレス・レーザー複合機、高速マウンタライン、放電加工機等々。これらは24時間稼働を行う機器なので、維持メンテナンスを行う事が大変重要な問題であったようです。オプションで稼働状況の見える化を行う事も出来ますが、機器毎に数千万単位の費用が発生してしまう。さらに、ラインが止まってから重度障害情報が出されたとしても時すでに遅いので、それ以前に設備の不調を把握し、事前に予防を行わなければならない課題があったようです。
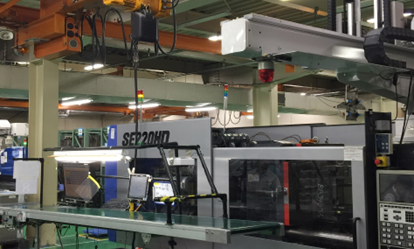
IoT導入により「小さな課題の見える化」を実現
2016年自社工場の製造機器に保全センサを設置し、実証実験を開始。異常値が出された後、専用のタブレットで対応状況をワンタッチで登録、停止項目や不良項目などその要因を登録する事で、稼働状況や稼働率、問題点ランキング等、モニター画面にリアルタイムで表示させ問題点の見える化を実現させました。
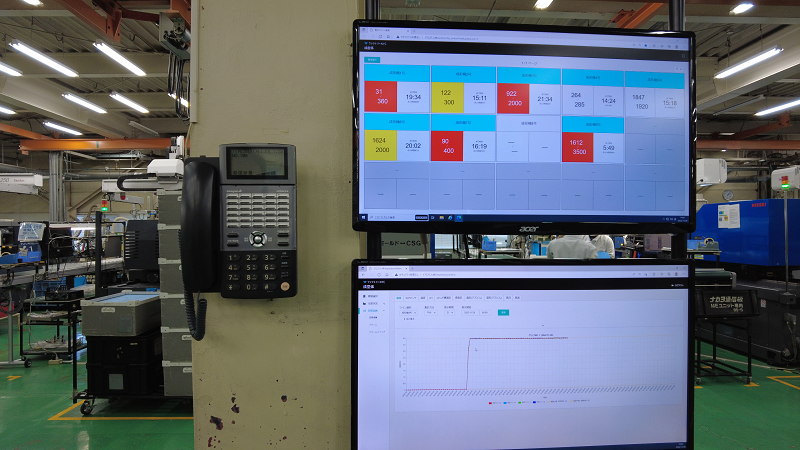
様々なセンシング
冷却ファンの風量監視
風量センサーによる冷却ファンのチェックを行い、異常値を検知した場合は、ファンの清掃や交換を実施する事で、温度上昇による設備本体の故障を未然に防ぐ効果を上げました。
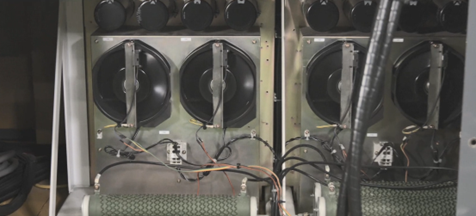
水漏れ監視
成型機の金型周りに漏液センサを設置し、水漏れが発生した際に作業者がいち早く気付くことができ、対処が可能となりました。
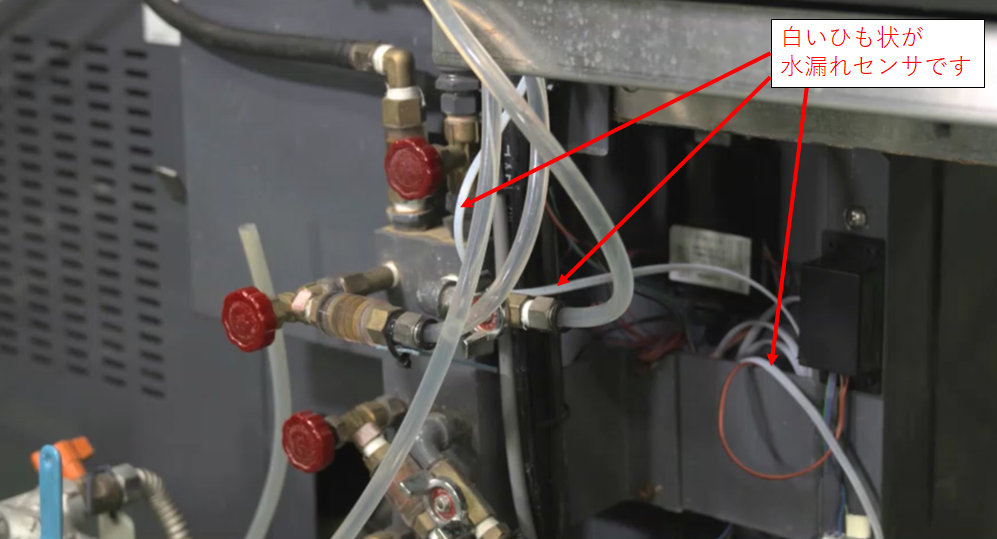
振動予兆検知
振動センサーと温度センサーの併用により、常に一定の振動値で動き続ける機械の異常値を把握し、経年劣化の監視に対応する事が可能となりました。
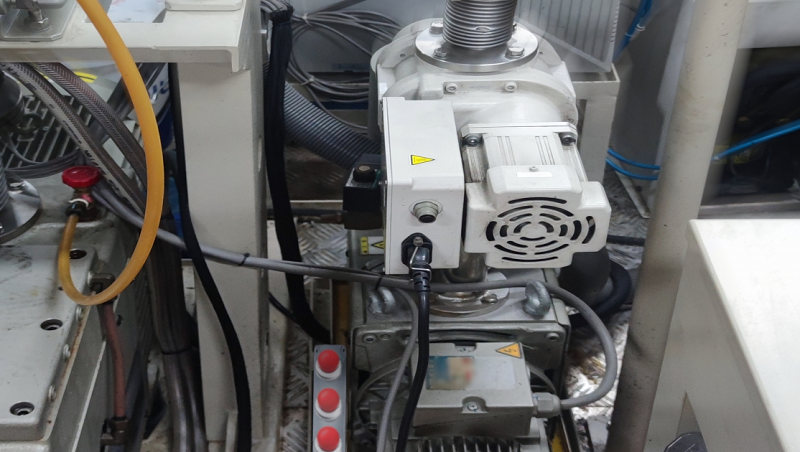
水質管理
板金洗浄機に導電計を追加し液汚れに関するデータ(pH、導電率)を見える化、液交換周期の適性化を図る事で、廃液処理にかかる費用を年間23%も低減することに成功したそうです。
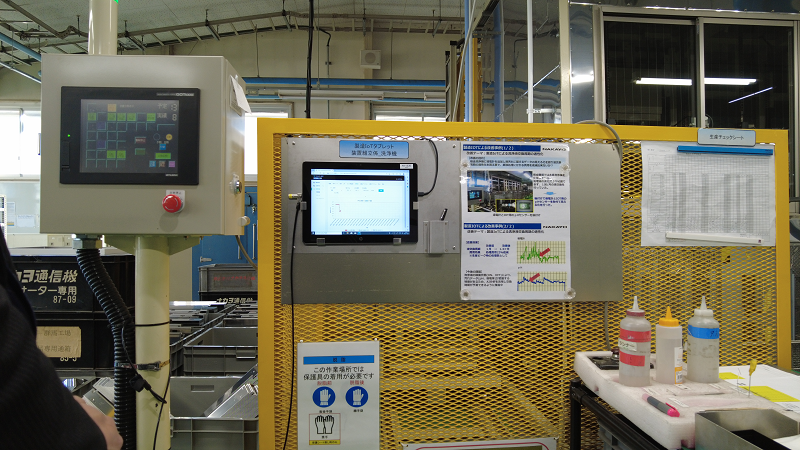
見学後記
株式会社ナカヨ様では、自社工場の稼働生産率を上げる為のカイゼンを実施しながら、IoT技術を活用した実証実験も継続して進めており、今回見学した設備に後付け、外付けでのセンシング以外に、今後はカメラを使った作業(人)の分析による改善や、ロボットの活用推進など進めらるようでありました。完全オートマチック化が出来ない製造ラインにおける人とセンシングとの融合、モノづくり日本の礎を支える企業であると感じました。
株式会社ナカヨ様 ファクトリーNYC概要はこちら
ご質問・ご相談に関しては
こちらからお問い合わせください。